Internet Explorer, Chrome Browser, Firefox Browser, Safari Browser
Press Release14 November 2017Digital Factory Frankfurt
Siemens presents seamless integrated solutions for additive manufacturing
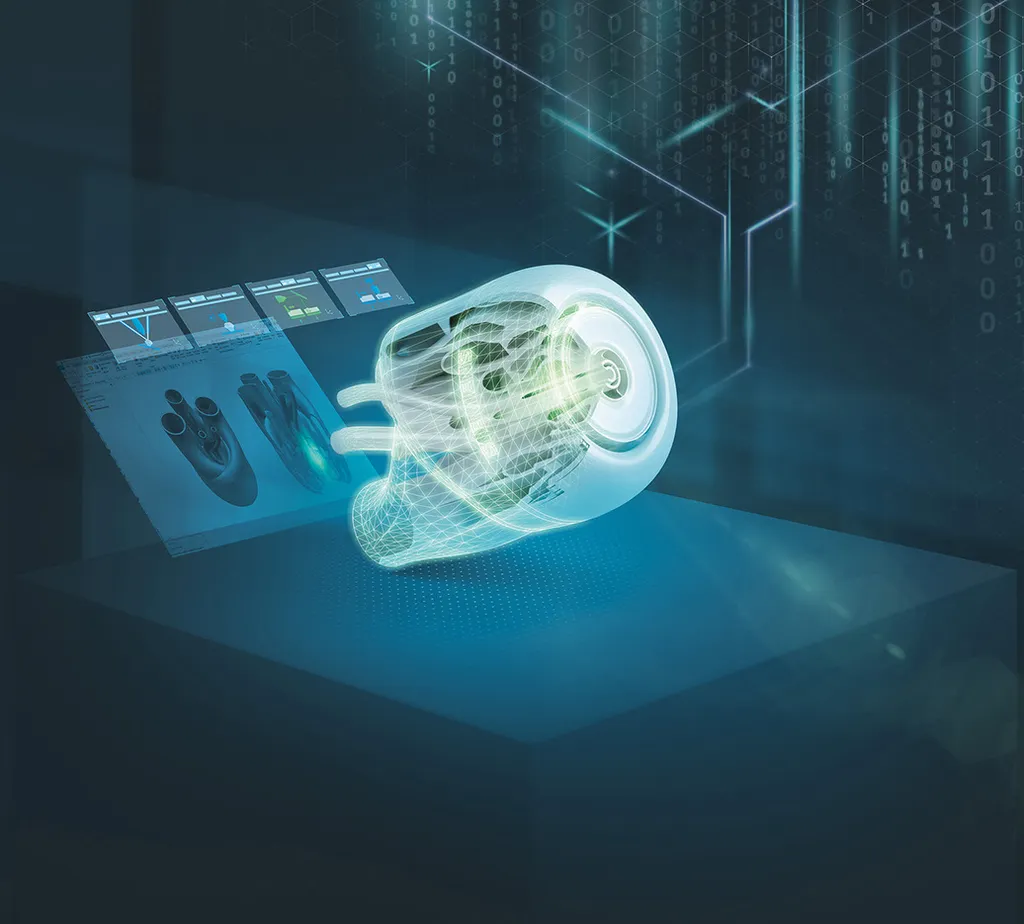
"Siemens is the world leading and only provider of integrated software and hardware solutions to cover every single phase of the value-adding process in the construction and utilization of AM machines. This means that today, we're already able to offer machine builders and users the chance to transition rapidly from prototyping and small production runs using single machines up to industrial scale volume production," explains Dr. Karsten Heuser, Vice President Additive Manufacturing, Center of Competence Digital Factory at Siemens AG.
Within the framework of its overarching "Digital Enterprise" concept, Siemens supplies a comprehensive portfolio for companies aiming to embrace the digital age. The Digital Enterprise Suite addresses the entire value chain and is based on Siemens PLM software solutions including NX™ software, an integrated CAD/CAM/CAE solution, the Simcenter™ portfolio, a suite of simulation software and test solutions, Teamcenter® software, the digital lifecycle management system, Simatic IT and Simatic WinCC, two elements of the Siemens Manufacturing Operations Management (MOM) portfolio for production execution and MindSphere, the cloud-based open Internet of Things (IoT) operating system. "What this means for machine builders and users is that the entire digital process chain is mapped out in a single integrated associative software environment which can consequently be operated using a standardized user interface. The tools used for engineering, simulation, production preparation and 3D printing are all grouped in a single cohesive system, eliminating the need for error-prone data conversion and the associated risk of losing information content," says Dr. Karsten Heuser.
"Siemens is the world leading and only provider of integrated software and hardware solutions to cover every single phase of the value-adding process in the construction and utilization of AM machines. This means that today, we're already able to offer machine builders and users the chance to transition rapidly from prototyping and small production runs using single machines up to industrial scale volume production," explains Dr. Karsten Heuser, Vice President Additive Manufacturing, Center of Competence Digital Factory at Siemens AG.
Within the framework of its overarching "Digital Enterprise" concept, Siemens supplies a comprehensive portfolio for companies aiming to embrace the digital age. The Digital Enterprise Suite addresses the entire value chain and is based on Siemens PLM software solutions including NX™ software, an integrated CAD/CAM/CAE solution, the Simcenter™ portfolio, a suite of simulation software and test solutions, Teamcenter® software, the digital lifecycle management system, Simatic IT and Simatic WinCC, two elements of the Siemens Manufacturing Operations Management (MOM) portfolio for production execution and MindSphere, the cloud-based open Internet of Things (IoT) operating system. "What this means for machine builders and users is that the entire digital process chain is mapped out in a single integrated associative software environment which can consequently be operated using a standardized user interface. The tools used for engineering, simulation, production preparation and 3D printing are all grouped in a single cohesive system, eliminating the need for error-prone data conversion and the associated risk of losing information content," says Dr. Karsten Heuser.
From product to production with Siemens PLM Software
In the constant drive to reduce component weight and improve resource usage, companies are looking to incorporate lattice structures into design in order to meet these goals without compromising on strength and structural integrity. The latest version of NX delivers new approaches to design for additive manufacturing, including the ability to add lattice. Convergent Modeling makes it possible to work directly with faceted geometry such as these lattice structures, saving companies from the lengthy data conversion process normally required. This enables companies to deliver lighter, stronger products to market in much less time. Used in combination with Simcenter, product characteristics can be simulated and predicted both in advance and during the course of the product life cycle – from the initial concept to the point of use. This accelerates product engineering, permits more affordable and reliable products to be brought to market and so helps to sharpen a company's competitive edge. The digital product life-cycle management system Teamcenter manages aspects such as product designs, documents, bills of material and data, allowing work and change processes to be standardized and efficiency to be optimized across the whole company.
Smart automation systems for additive manufacturing
When it comes to the industrialization of additive manufacturing, the smart automation of production systems has a decisive role to play. At formnext 2017, Siemens will be demonstrating how automation solutions for industrial AM systems are able to monitor motion control, optimize processes and so enhance availability, IT security, quality and productivity. Underpinning this are PLC-based automation solutions using Simatic or CNC-based automation solutions with Sinumeric. These work in combination with Sinamics drive systems and Simotics motors to move mechanical units of the machine. With its Totally Integrated Automation (TIA) Portal, Siemens enables all of these automation components to work efficiently together. Other topics featured at the Siemens formnext booth include digitalization and the management of additive manufacturing with Simatic IT UA as well as data protection and user rights management.
Linking AM machines to the Internet of Things
With MindSphere, Siemens will be demonstrating its cost-efficient scalable cloud "Platform as a Service". Designed as an open operating system, MindSphere enables a seamless connection between the machine and the digital world. By using extensive volumes of data, machine builders and producers can achieve greater productivity and efficiency throughout the entire company, reducing downtimes, boosting production and enabling more effective plant utilization. At the same time, MindSphere offers seamless connectivity between the data-based services offered by Siemens and those of third-party providers. A manufacturer's own apps and services can also be seamlessly integrated.
Boosting the speed of additive manufacturing industrialization with innovative value-add services
For the first time at the formnext, Siemens will be showcasing a modular suite of consulting services designed to help customers speed up the industrialization of additive manufacturing. The service draws on expertise taken from different Siemens units and concentrated within the framework of its group-wide additive manufacturing innovation field, from design through the development of business models to production – all from a single source.
Engineering and printing services through to the complete additive manufacturing of parts with Material Solutions and Mobility Services
Siemens recently provided impressive proof of its command of additive manufacturing with the successful printing and application of gas turbine blades. This expertise is now being made available to other sectors of industry as a manufacturing service through the Siemens subsidiary Materials Solutions – from the idea through to printing of the finished components.
For further information on topic Siemens at the formnext 2017, please see www.siemens.com/presse/formnext2017 and www.siemens.com/formnext
For this press release
Siemens AG (Berlin and Munich) is a global technology powerhouse that has stood for engineering excellence, innovation, quality, reliability and internationality for 170 years. The company is active around the globe, focusing on the areas of electrification, automation and digitalization. One of the world's largest producers of energy-efficient, resource-saving technologies, Siemens is a leading supplier of efficient power generation and power transmission solutions and a pioneer in infrastructure solutions as well as automation, drive and software solutions for industry. The company is also a leading provider of medical imaging equipment – such as computed tomography and magnetic resonance imaging systems – and a leader in laboratory diagnostics as well as clinical IT. In fiscal 2017, which ended on September 30, 2017, Siemens generated revenue of €83.0 billion and net income of €6.2 billion. At the end of September 2017, the company had around 372,000 employees worldwide. Further information is available on the Internet at www.siemens.com.
Reference Number: PR2017110065DFEN
Contact
Katharina Lamsa
Siemens AG
Gleiwitzer Str. 555
90475 Nuremberg
Germany
90475 Nuremberg
Germany
+49 (911) 895-7975