Internet Explorer, Chrome Browser, Firefox Browser, Safari Browser
Press Release13 September 2017Digital Factory Nuremberg
CNC-integrated robot kinematics optimizes control of robot-aided machining tasks
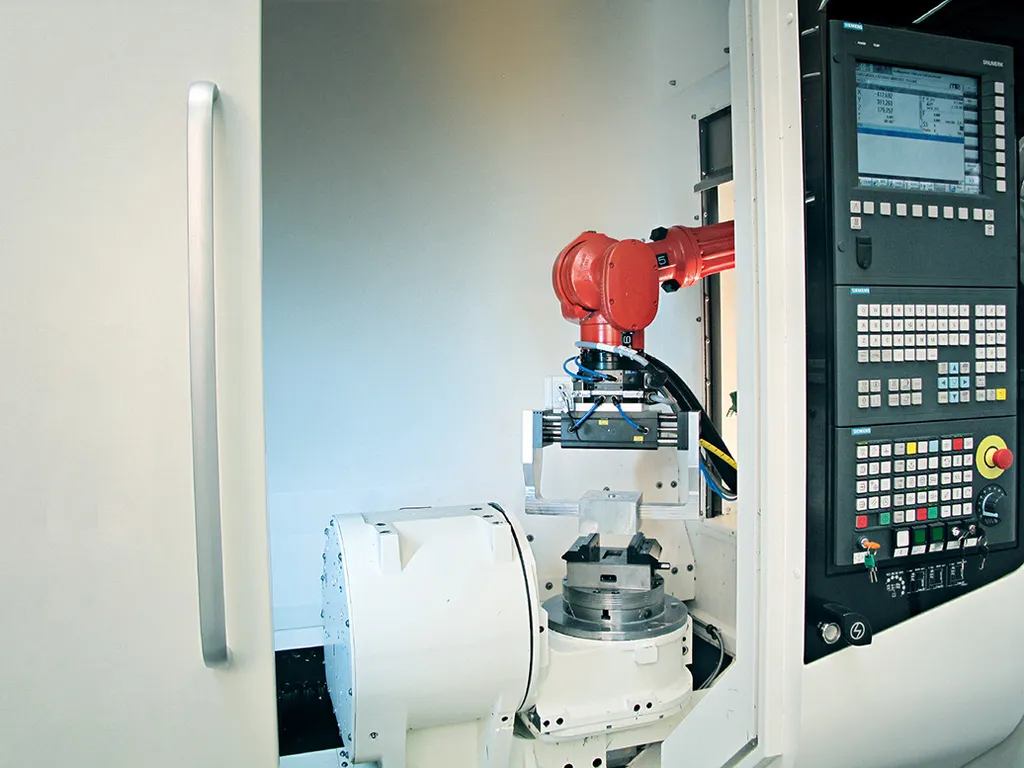
Integrating control of the robot arm into the CNC control loops helps improve path and positioning accuracy as well as reliability. This also makes for an enhanced dynamic response during robot-aided machining tasks. As a result, the robot is able to undertake more challenging machining assignments and users enjoy the advantages of compact hardware, simple engineering, and quick commissioning. Some Industrial sectors benefiting from the use of Sinumerik Run MyRobot /DirectControl include additive manufacturing, fiber placement, metal cutting, carbon fiber-reinforced polymer, and laser machining.
The major difference between the new /DirectControl technology and conventional solutions is that /DirectControl performs all the functions previously assigned to the robot control system. This makes the robot controller not required. Apart from this underlying difference, Sinumerik Run MyRobot /DirectControl performs all the same functions as the previous Run MyRobot variants. The new solution not only enables more dynamic application of the robot, but also makes for tighter control, improves capacity for robot operations to run parallel with machining time.
To simplify the engineering process, complete configuration for all /DirectControl supported robot arms is stored in the Siemens engineering tool Sizer. The same high level of convenience is offered when it comes to robot commissioning: Data sets for the relevant mechanics are made available by the robot manufacturer COMAU and simply imported in a channel of the Sinumerik CNC.
There is also practical support for other engineering functions; Digital twins are available for /DirectControl-compatible COMAU robot arms to enable work in NX CAM Robotics. The kinematic 3D robot model and the virtual NC kernel Sinumerik VNCK enable subprograms generated in the CAD-CAM chain to be realistically simulated. Additional benefits to the simple operation are the reduced footprint due to the elimination of hardware components, lower investment, reduced stocking costs for spare parts, and greater availability due to improved MTBF (Mean Time Between Failures).
For further information about Siemens at the EMO Hannover 2017 please see www.siemens.com/emo and www.siemens.com/press/emo2017
For further information about Siemens at the EMO Hannover 2017 please see www.siemens.com/emo and www.siemens.com/press/emo2017
For this press release
Siemens AG (Berlin and Munich) is a global technology powerhouse that has stood for engineering excellence, innovation, quality, reliability and internationality for more than 165 years. The company is active in more than 200 countries, focusing on the areas of electrification, automation and digitalization. One of the world's largest producers of energy-efficient, resource-saving technologies. Siemens is a leading supplier of efficient power generation and power transmission solutions and a pioneer in infrastructure solutions as well as automation, drive and software solutions for industry. The company is also a leading provider of medical imaging equipment – such as computed tomography and magnetic resonance imaging systems – and a leader in laboratory diagnostics as well as clinical IT. In fiscal 2016, which ended on September 30, 2016, Siemens generated revenue of €79.6 billion and net income of €5.6 billion. At the end of September 2016, the company had around 351,000 employees worldwide. Further information is available on the Internet at www.siemens.com.
Reference Number: PR2017090402DFEN
Contact
Katharina Lamsa
Siemens AG
Gleiwitzer Str. 555
90475 Nuremberg
Germany
90475 Nuremberg
Germany
+49 911 895-7975