Internet Explorer, Chrome Browser, Firefox Browser, Safari Browser
Press Release20 April 2017Process Industries and DrivesNuremberg
Plug & Play for process automation – integrated engineering out-of-the-box
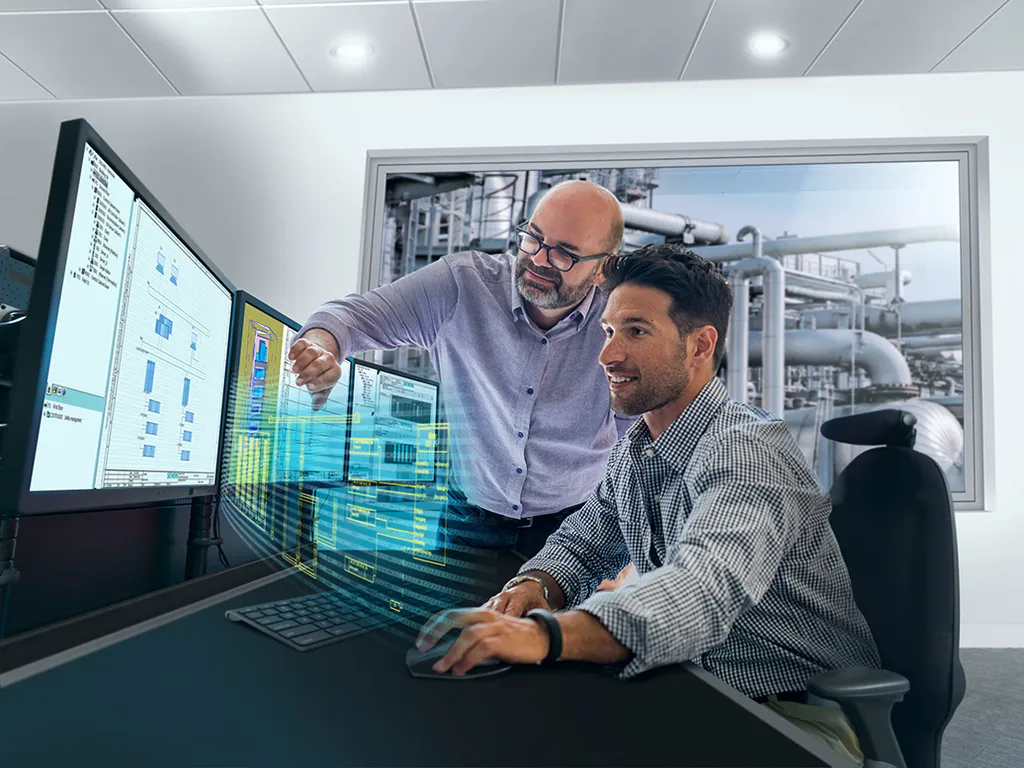
Plug & Play for process automation – integrated engineering out-of-the-box
The large number of entities, data formats and interfaces involved means that process plant engineering workflows are often prone to transmission errors and system conflicts. Information can frequently go missing or have to be manually corrected during data exchange between different disciplines. This increases the time required for engineering and the costs involved. The object-oriented approach of the Simatic PCS 7 Plant Automation Accelerator enables users to work on a central data platform, guaranteeing completely integrated planning based on an electronic workflow, starting with plant engineering through to automation.
All the planning data of a project exists in the central data model of the Simatic PCS 7 Plant Automation Accelerator. Automation specialists have access to functions required for the compilation of quotations such as bills of material and automatically generated control data from the electrical plans of the Siemens Simatic PCS 7 process control system, including controlled mass data engineering, through to as-is process automation documentation. Use of the Simatic PCS 7 Plant Automation Accelerator not only boosts project efficiency but also minimizes risks. The high level of standardization and tool-supported configuration additionally save time and engineering costs during the project phases. Simple synchronization between planning and automation data helps prevent the double input of data and interface losses, as well as significantly reducing project lead times.
The Simatic PCS 7 Plant Automation Accelerator builds a digital bridge between plant planning and the Simatic PCS 7 process control system. The tool enables integrated engineering across the entire life cycle of an industrial plant – at the same time minimizing the number of interfaces. At the press of a button, the entire plant structure is generated in the control system from the engineering data. Controlled mass data engineering and simple, consistent change management help to raise the standard of quality, simplifying the engineering process and substantially reducing the amount of time required. Changes occurring in the automation system during running operation, for instance following an exchange of field devices, can be played directly back into the planning software. At the same time, the database in the engineering tool is immediately updated, and along with it the entire plant documentation.
To speed up the Factory Acceptance Test (FAT), it can often be beneficial to generate a simulation of the plant prior to commissioning and so minimize the error quota. Data such as measurement points and signals of a digital plant can be exported over the Simatic PCS 7 Plant Automation Accelerator to the Siemens simulation tool Simit, allowing a digital twin of the plant to be generated.
Data synchronization of the control system and planning automatically produces seamless, up-to-date plant documentation, providing sustainable investment security for future plant upgrades and migration processes, both for existing and new plants.
For this press release
Siemens AG (Berlin and Munich) is a global technology powerhouse that has stood for engineering excellence, innovation, quality, reliability and internationality for more than 165 years. The company is active in more than 200 countries, focusing on the areas of electrification, automation and digitalization. One of the world's largest producers of energy-efficient, resource-saving technologies, Siemens is a leading supplier of efficient power generation and power transmission solutions and a pioneer in infrastructure solutions as well as automation, drive and software solutions for industry. The company is also a leading provider of medical imaging equipment – such as computed tomography and magnetic resonance imaging systems – and a leader in laboratory diagnostics as well as clinical IT. In fiscal 2016, which ended on September 30, 2016, Siemens generated revenue of €79.6 billion and net income of €5.6 billion. At the end of September 2016, the company had around 351,000 employees worldwide. Further information is available on the Internet at www.siemens.com.
Reference Number: PR2017040250PDEN
Contact
Evelyne Kadel
Siemens AG
Klaus-Bungert-Str. 6
40468 Dusseldorf
Germany
40468 Dusseldorf
Germany
+49 (211) 6916-1003